在当今追求高效节能与健康理疗并重的时代,石墨烯发热技术以其革命性的突破成为市场焦点。作为国内少数掌握石墨烯涂层核心技术的企业,归壹石墨烯发热片源头工厂通过自主研发的蜂窝结构配方,将电热转化率提升至99%的行业巅峰,相比传统金属丝、碳纤维等发热材料实现节能30%-50%的跨越式进步。这种以单层碳原子六边形晶格为基础的新型材料,不仅具备超强的导热导电性能,其释放的8-14μm远红外生命光波更与人体细胞分子振动频率高度契合,能深层渗透皮肤组织产生共振效应,促进血液循环并缓解关节疼痛——这使产品在电热功能之外,更被广泛应用于医疗康复、健康家居等理疗场景。
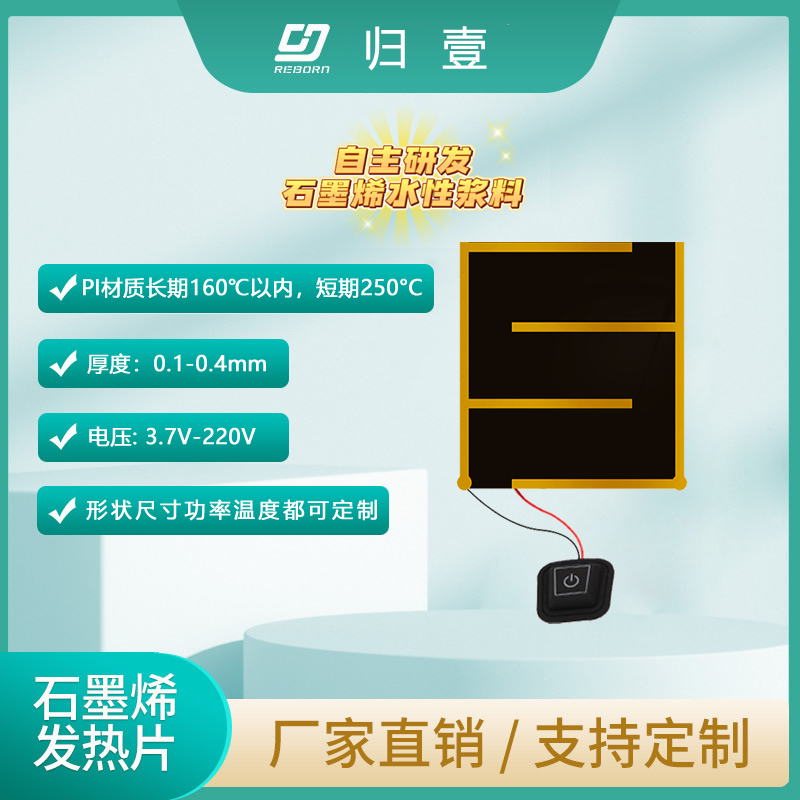
工厂的研发实力体现在对多元基材的深度适配能力上。针对不同行业需求,团队开发出七大类基材解决方案:PI薄膜耐高温达200℃且柔韧性强,适用于汽车座椅加热等精密工业场景;PET材料成本优势明显,是暖宫宝、电热护膝等消费级产品的理想选择;TPU基材兼具弹性和防水性,可植入滑雪服、潜水装备等特殊服饰;而硅胶基材则凭借生物相容性成为医疗热敷贴的首选。更值得一提的是独创的金属基复合发热板,通过石墨烯与铝合金的分子级结合,解决了传统金属加热器局部过热难题,在工业烘干领域实现温度波动±1℃的精准控制。
在安全性能方面,工厂突破性采用梯度电压设计技术。常规产品工作电压覆盖人体安全范围的3.7V-36V,特别开发的48V-220V高压系列则通过多层绝缘封装工艺,确保在电动汽车电池预热、管道防冻等工业场景中绝对安全。所有产品均通过ISO9001质量体系认证,并获得RoHS、CE等国际安全认证,其独创的"三明治"防护结构将漏电流控制在0.01mA/cm²以下,远超行业标准。某知名家电品牌采用该技术后,电热毯产品连续工作2000小时无衰减,使用寿命较传统产品延长3倍。
定制化服务构成工厂的核心竞争力。从设计端开始,工程师团队可提供3D热力仿真分析,确保异形发热片(如螺旋状、镂空图案等)的温度均匀性。曾为航天领域开发的环形加热膜,在-40℃极寒环境下仍保持快速响应,升温至80℃仅需18秒;而为智能马桶盖定制的波浪形电热膜,则实现0.1mm超薄厚度与98%的热均匀度双重突破。生产线上配备激光精密切割系统,能实现最小0.5mm的线宽精度,满足医疗美容仪器等微型化设备的苛刻要求。
在应用场景拓展方面,工厂的创新案例持续刷新行业认知。与农业科技公司合作的植物培育加热板,通过石墨烯远红外促进种子发芽率提升40%;为极地考察队设计的自加热服装系统,在-50℃环境中维持人体核心温度的同时,整机重量减轻60%;最新研发的透明导电发热膜已应用于新能源汽车前挡风玻璃除霜,透光率超85%且电阻值稳定在50Ω/sq。这些突破源自对石墨烯浆料配方的持续优化——通过调控纳米银线掺杂比例和石墨烯氧化物还原度,使发热体电阻温度系数(TCR)控制在±50ppm/℃的极窄范围。
环保属性是产品的另一重要维度。整个生产流程采用水性分散工艺,实现VOCs零排放;发热片废弃后可自然降解率达92%,较传统电热材料减少70%的环境负荷。某国际运动品牌在可持续发展报告中特别指出,采用该工厂石墨烯加热技术的滑雪靴,单季度减少碳排放达1.2吨。这种绿色制造理念与蜂窝结构带来的材料节省效应,使产品在全生命周期都体现着节能环保优势。
面对智能物联时代的新需求,工厂率先将IoT模块集成到发热系统中。最新发布的智能温控系列支持蓝牙/Wi-Fi双模连接,用户可通过手机APP实现0.1℃精度的分区控温,历史数据记录功能还可为理疗效果提供量化参考。为智能家居开发的隐形地暖膜,厚度仅0.3mm却具备200W/m²的功率密度,配合AI学习算法可节省采暖能耗45%。这些智能化升级背后,是研发中心每年超15%的营收投入和23项发明专利的强力支撑。
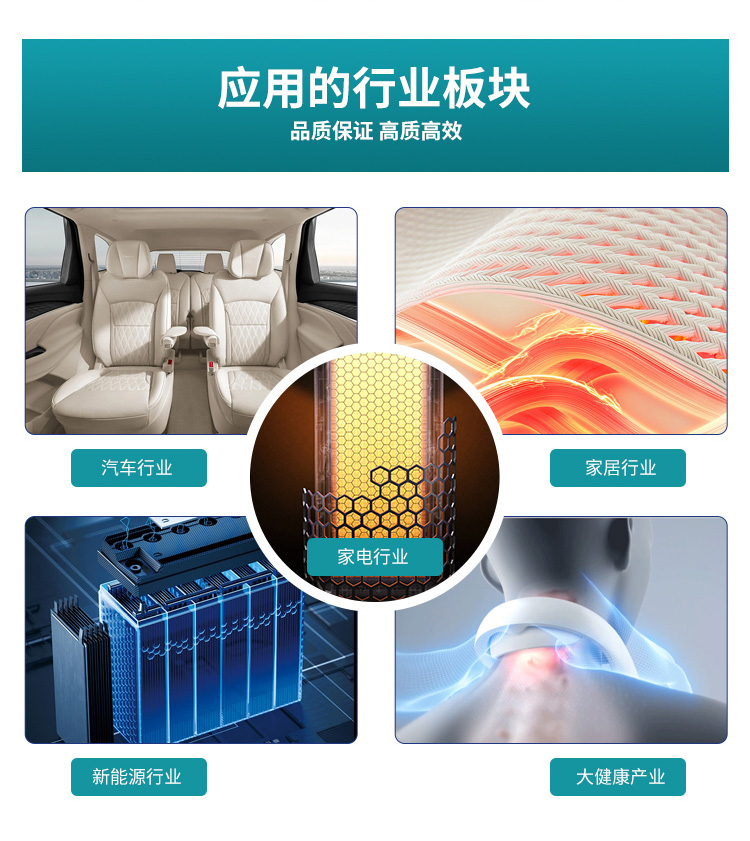
从医疗康复到航空航天,从智能穿戴到工业装备,归壹石墨烯发热片正重新定义热能转换的边界。其核心价值不仅在于突破性的节能表现,更在于将尖端材料科学转化为改善人类生活的实际方案。随着第五代石墨烯量子点涂层技术的试验成功,未来发热效率有望进一步提升至99.5%,这项源自中国制造的创新科技,正在全球热管理领域书写新的标准。